Press release
Related Press
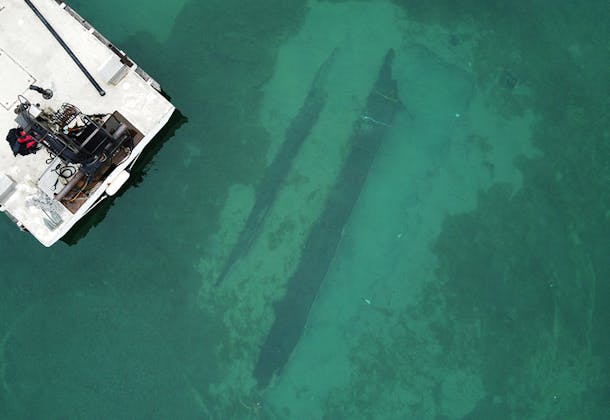
5 October 2020
A new Roman shipwreck discovered in Switzerland
CSEM engineers have used new lidar technology to analyze the ruins of a Roman shipwreck in Lake Neuchâtel. Their method generates 3D images in just a few seconds, enabling archeologists to visually an...
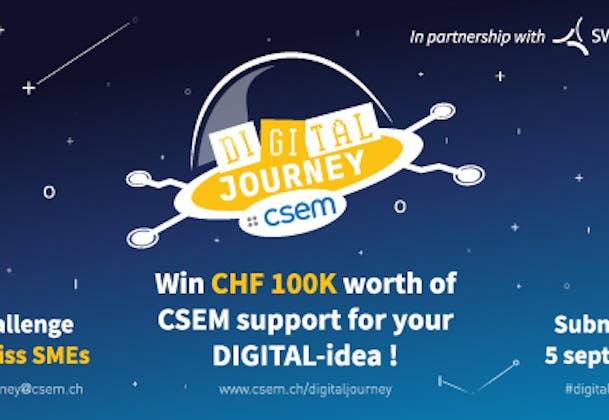
8 June 2022
CSEM launches the fifth edition of its Digital Journey
CSEM launches the fifth edition of its "CSEM Digital Journey" competition, which has been explicitly developed for Swiss SMEs....
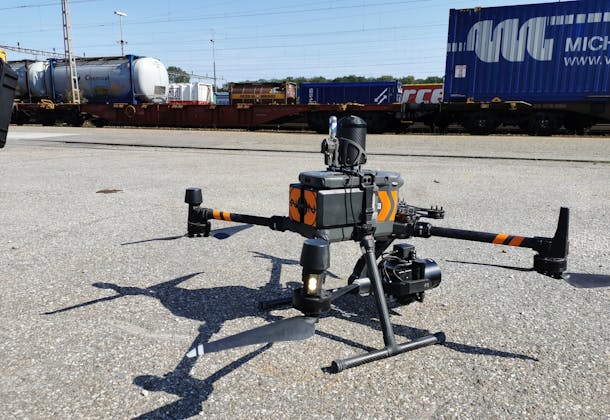
29 August 2024
A high-tech 'neophyte radar': Using drones and AI to detect invasive plants
Invasive alien plants are a threat to our environment. A research initiative is now tackling the problem: The Neophyte Radar will detect the invaders from the air and enable effective containing....