May 1, 2018
Paving the way for printed optical circuits
At a time when optical components are critical enabling technologies in so many fields, from sensors to wearable devices and data transfer to healthcare applications, there is a compelling need to find new techniques for miniaturized, precision production. CSEM has developed a promising method using inkjet printing - an attractively adaptable but until now challenging option.
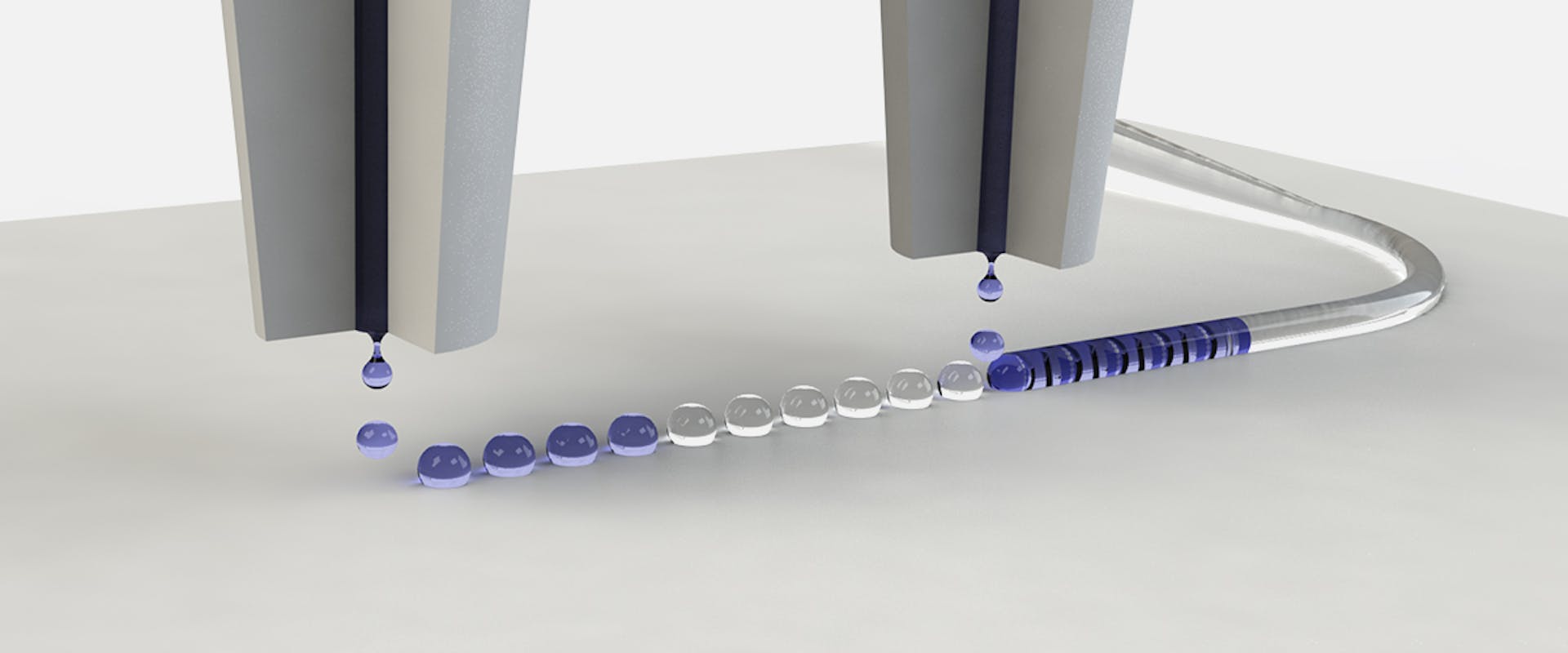